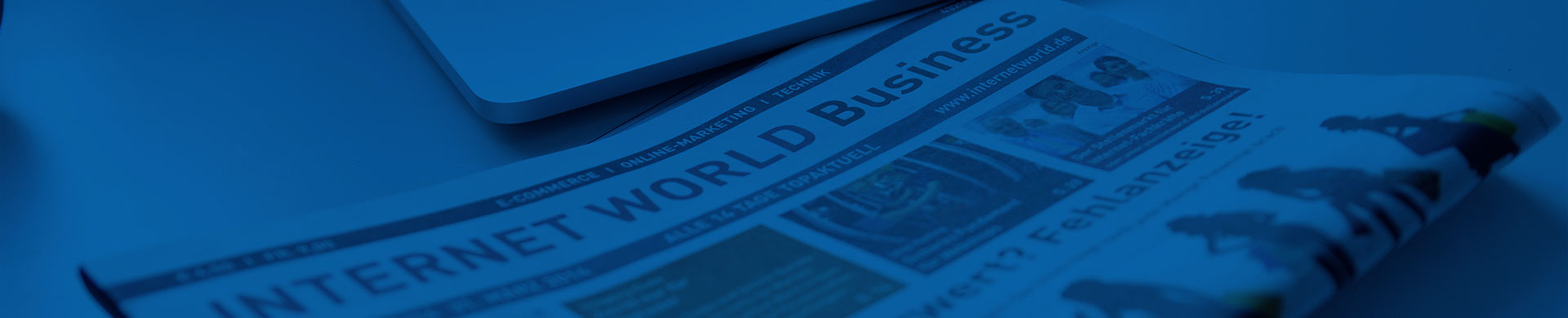
Recently, the 1,000,000tpa high speed bar EPC project contracted by Sinosteel MECC for Shanxi Jianbang Group Co., Ltd. (Jianbang Group) started production and successfully reached the designed capacity.
The maximum continuous rolling speed of the project reaches 45m/s, and the stable rolling speed reaches 42.75m/s. The main technical indicators have reached the first-class level in the industry. Adopting the world's first extra-heavy-duty 330mm modular rolling mill three-level controlled rolling process, Sinosteel MECC has achieved another successful cooperation with Jianbang Group.
▲ On the completion ceremony, Tang Faqi (second from right), Deputy General Manager of Sinosteel MECC, and the team took photo with representatives of Jianbang Group.
Multiple self-developed technologies
Rolling speed reaches 45m/s
The product mix of the high speed bar EPC project contracted by Sinosteel MECC is Φ12.0mm-Φ25.0mm deformed bar, and the capacity is 1,000,000 tpa. The project adopts self-developed bar system rolling technology and equipment of Sinosteel MECC, including three-level controlled rolling and controlled cooling process, extra-heavy-duty 330mm modular rolling mill, large type high speed flying shear, high speed bar loading system, etc. Adopting continuous casting direct rolling technology, heating furnace is not used in the full technology design, which is another new technology revolution in Jianbang Group's product technology upgrading and cost reduction.
The project was successfully hot commissioned on November 30, 2021. During the hot commissioning, the maximum rolling speed reached 45m/s, and then it maintained stable and efficient operation with a rolling speed of 42.75m/s. The rolling mill line adopts “one line and one room” and centralized control, which greatly improves the work efficiency and effectively reduces production quota in the rolling mill line.
Advanced technology
Cost reduction & efficiency increase
Green and low-carbon
The project has adopted a number of self-developed technologies of Sinosteel MECC, especially the first extra-heavy-duty 330mm modular rolling mill’s double heat engines rolling process in the world, which has many significant advantages and has opened a new era for high speed bar production line.
High speed zone modular rolling mill
“2+2+2” process layout
Based on the "4+2" process layout developed by Sinosteel MECC, the project team optimized and adjusted the product mix of the existing production line and the overall layout of the workshop according to local conditions, and further developed the "2+2+2" extra-heavy-duty 330mm modular rolling mill controlled rolling process. This process not only solves the problems of the traditional high speed bar production line, such as the easily explosive roll of the finishing ring rolling mill, the low rolling speed, and the limited product specification range, but also achieves "three betters":
◆ Greater rolling force (up to 50 tons)◆ Wider product diameter range (φ10mm-φ32mm)
Controlled rolling and cooling technology & equipment
Cost reduced by RMB 100 per ton of steel
The project also adopted Sinosteel MECC’s self-developed controlled rolling and controlled cooling process technology and equipment. While improving the internal organization and increasing the strength of the steel bar, the grain size grade of the product can be increased by 2 grades to achieve cost reduction and efficiency increase for customers: Diameters Ф12mm to Ф25mm deformed bar alloy manganese content is less than 0.8-1.2% respectively, and vanadium, niobium and other strengthened alloy elements are not added, reducing cost by RMB 100 yuan in producing a ton of steel.
Heating furnace-free direct rolling
Saving 3000m3/hour of natural gas
The project utilizes the heating furnace-free direct rolling technology developed by Sinosteel MECC, which increases the temperature and conveying speed of the continuous casting billet, ensures the direct rolling rate, eliminates the loop between casting and rolling, and makes the steelmaking and rolling workshops a closely connected integrated production system.
According to preliminary calculation by the developing team of the project, about 3000m3/hour of natural gas can be saved during production. As the fuel for heating furnace is largely reduced, the project can reduce energy consumption and carbon dioxide emissions, improve metal yield, shorten production cycle, improve product quality, reduce area occupancy of the product, save manpower, and reduce investment at the same time.
After successfully putting into production, the stable rolling speed of 42.75m/s breaks the speed record of the previous full continuous high speed bar rolling system key technology. This is a new breakthrough in Sinosteel MECC’s self-developed bar rolling technology and equipment, as well as a new achievement of Sinosteel MECC in providing optimal solutions and services to customers. The project not only helps Jianbang Group realize its strategic layout, but also consolidates the pioneering position of Sinosteel MECC in the field of bar rolling technology.