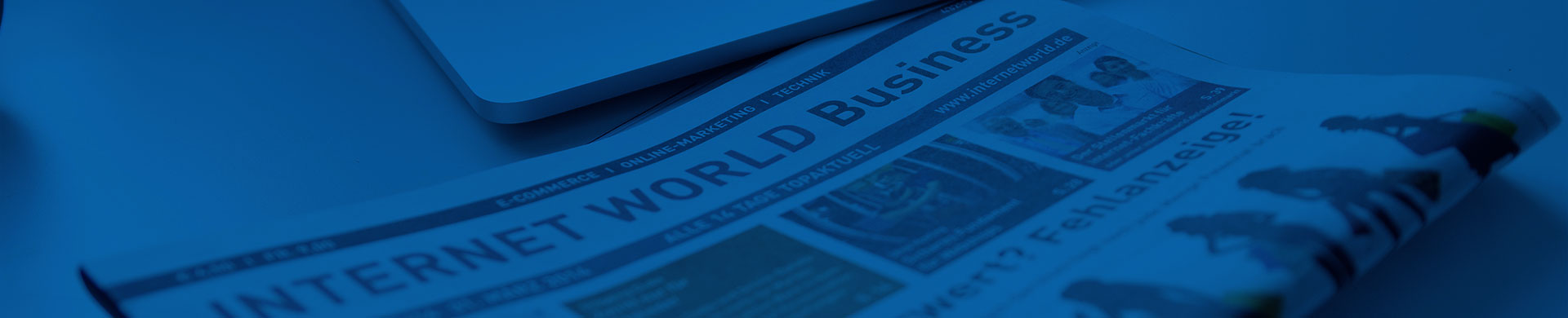
Duration: 2006-2008
Main technical features:
circular cooler area was increased to 360m2 considering the less effectiveness of 280m2 circular cooler for 265m2 sinter machine when hot screen was removed;
cancellation of hot screen has improved production continuity and discharge end environment, reduced main building platform level and resistance loss of main exhaust system;
process interlocking & centralized control and utomatic monitoring to critical equipments used for all system equipments have considerably improved control level of production process;
automatic proportioning: to improve stability of proportioning and realize process detection and control, electronic belt weigher (proportioning accuracy ±1%) was used to meter and control iron material, coke fine, dolomite and quicklime by weight ratio.
sintering with all quick lime increased material temperature by taking use of the heat from quicklime slaking and improved the mixture granulation effect;
600℃~800℃ hot waste gas from gas heating furnace was inducted to mixing and granulating machine to increase temperature of mixed material by more than 10℃;
granulation effect was improved by increasing mixer length, extending time of mixing and granulating to 8.68 minutes, and adjusting rotation speed (0 ~ 7.5r/min) of granulating machine with hydraulic coupler;
infrared moisture measurement device was used to detect mixed material and automatically add moisture;
10mm ~ 20mm sinter after size stabalization were layed to thickness of 30mm ~ 40mm on pallet, which increased brethability of bedding and prevented bar grates from sticking and melting;
deep-bed sintering - thickness of material layer was 700mm (including bedding 30 ~ 40mm);
sinter flue gas was inlet to main exhaust fan through 2 ducts and effective measures were taken to reduce mutual interference of the two fans and increase gas volume;
dust of fume duct and electrostatic precipitator were discharged to belt converyor through electric hydraulic double valves and then transported No.1 proportioning room;
wearing resistance material was coated to inner side of fume duct and wind box and heat insulation layer (δ=100mm) to outer side, to ensure leakproofness of air system;
apron feeder replaced electric vibrating feeder below the circular cooler discharging hopper;
dust from sintering process was recycled and moistured to reduce reentrainment;